Medartis AG
1.2 Cortical Screw 11mm, HD4, 5/Pkg
Cleaning, Disinfection, Sterilization, Inspection and Maintenance Instructions
41 Pages
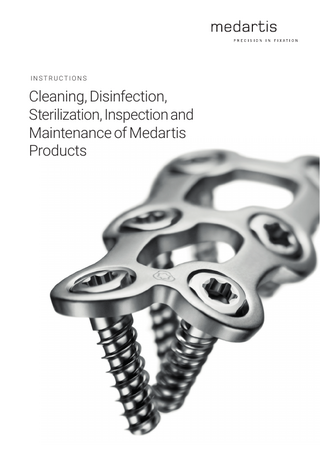
Preview
Page 1
INSTRUCTIONS
Cleaning, Disinfection, Sterilization, Inspection and Maintenance of Medartis Products
2 l Cleaning, Disinfection, Sterilization, Inspection and Maintenance of Medartis Products
Contents 1
Introduction 3
2
General Basics 3
2.1
Shipment 3
2.2
Reuse of Medartis Products
2.3
Assembling/Disassembling (Instruments) 3
2.4
Materials 3
2.4.1
Material Durability 3
3
Basics for Cleaning, Disinfection and Sterilization
3
of Medartis Products 4 4
Flowchart 5
5
Preparing for Cleaning, Disinfection and Sterilization
5
5.1
Segregating and Preparation of the Instruments after Surgery
5
5.2
Pretreatment for Cleaning, Disinfection and Sterilization
5
6
Cleaning and Disinfection 6
6.1
Manual Cleaning and Disinfection
6
6.2
Automated Cleaning and Disinfection
7
7
Inspection and Maintenance 7
7.1
Inspection 7
7.2
Care and Maintenance 8
8
Packaging 8
9
Sterilization 9
10
Storing 9
11
Symbols 9 APPENDIX
For further information regarding the Medartis products, visit www.medartis.com
medartis.com
Cleaning, Disinfection, Sterilization, Inspection and Maintenance of Medartis Products l 3
PLEASE CAREFULLY READ AND FOLLOW THESE INSTRUCTIONS
Products that have not come into direct contact with a patient may be reprocessed. Products which are not labelled with the above mentioned symbol may be reused. These products include instruments, 1 INTRODUCTION trays/container under the prerequisite that these products are undamaged and clean. These reusable products have to be This document, “Instructions for Cleaning, Disinfection, reprocessed before each use. Sterilization, Inspection and Maintenance of Medartis In case of disregard of these instructions, the manufacturer Products” includes information about: excludes any liability. • the reprocessing (cleaning, disinfection and sterilization) of products from Medartis • the inspection and maintenance of the instruments • the identifying features relating to wear/tear and loss of usability
Medartis defines no maximal number of reuses for reusable products. The life-cycle of the products depends on many parameters, e.g. the way and duration of the individual usages, and/or the handling, the treatment between the usages. Careful inspections and functionality tests of the products before each usage are the best methods to affect the products’ lifetime. Additional information about the products is provided in the “In- Medartis recommends using twist drills and reamers only for structions for Use”, individual product brochures and surgical a maximum of ten times. techniques. Any information can be requested at any time from your local Medartis territory consultant or distribution partner. 2.3 Assembling/Disassembling (Instruments) In addition, all relevant information can be found on the internet To insure that instruments undergoing cleaning/disinfection at: can be properly assembled/disassembled, attention has to be www.medartis.com/documentation/instructions-for-use. paid to the individual “Assembly/Disassembly Instructions” The reprocessing of the products (cleaning-, disinfection- and provided separately at www.medartis.com/documentation/ sterilization process) which is described in this document was instructions-for-use. Please keep in mind that instruments which are not represented tested and validated by Medartis. in the “Assembly/Disassembly Instructions” are not intended In the following text the term “products” covers: to be disassembled. - implants 2.4. Materials - instruments - trays/containers Product Material In case of different handling, the sub-groups are explicitly mentioned. Plates Pure titanium, titanium alloy 2
GENERAL BASICS
2.1 Shipment All components that are delivered NON-STERILE must be appropriately cleaned, disinfected and sterilized before each use. This also applies to the first use after delivery (after removal of the protective transport packaging). 2.2 Reuse of Medartis Products Medical devices which are intended for single use are labelled with the following symbol: These products are intended for one single application in a single patient. They must be cleaned, disinfected and sterilized before use.
Wedges
Titanium alloy
Spiral blades
Pure titanium
Washers
Pure titanium, titanium alloy
Screws
Titanium alloy
Staples
Stainless steel
K-wires
Stainless steel
Instruments
Stainless steel, PEEK, aluminum, Nitinol, silicone or titanium
Containers
Stainless steel, aluminum, PEEK, polyphenylsulfone, polyurethane, silicone
Repeated reprocessing cycles as described in these instructions have negligible effects on Medartis products. Testing prior to sterilization can be required to ensure proper function. The method for the functional testing, when applicable for the implant or instrument, is provided in these instructions.
2.4.1 Material Durability All Medartis products can be exposed to temperatures up to a maximum of 141°C (286°F). When choosing detergents and disinfectants the following warnings must be respected:
Implants that were used in a patient and removed have to be discarded following the local requirements. They may not be reused. Re-use may compromise the structural integrity of the implants and/or lead to device failure which may result in patient injury. Furthermore, re-use of single-use devices may create a risk of contamination e.g. due to the transmission of infectious material from one patient to another. This could result in injury of the patient or user. Implants that have come in direct contact with blood or other bodily fluids or show visual contamination must be cleaned and disinfected separately before they can be placed back into the implant tray.
Material
Not recommended
Aluminum (anodic oxidation etc.)
► Alkaline or ingredients containing iodine or salts of heavy metal (e.g. mercury) ► Poor water quality, alkaline cleaning agents, acidic neutralizers
medartis.com
4 l Cleaning, Disinfection, Sterilization, Inspection and Maintenance of Medartis Products
Color coding
► All oxidating acids (e.g. nitric acid, acid sulphur, oxalic acid), H2O2 (hydrogene peroxide) ► Excessive concentrations of cleaning and disinfection agents
Stainless steel
► Elevated chlorine concentration ► Oxalic acid ► H2O2 (hydrogene peroxide)
Titanium
► All oxidating acids (e.g. nitric acid, acid sulphur, oxalic acid), H2O2 (hydrogene peroxide)
3
BASICS FOR CLEANING, DISINFECTION AND STERILIZATION OF MEDARTIS PRODUCTS
The basics which are described in this chapter have to be followed for all reprocessing steps! Thorough cleaning and disinfection are essential for an effective sterilization. Two methods, a manual and an automatic method, are described for the cleaning/disinfection of the Medartis products. If possible an automatic procedure (disinfector) must be used. A manual procedure even with an ultrasonic bath is significantly less effective.
(such as approval by VAH/DGHM or a CE mark) • the detergents and disinfectants must be suitable and compatible for use with the products (please see also chapter 2.4 “Materials”) • the manufacturers’ instructions, such as those regarding concentration, exposure time and temperature, must be followed Medartis recommends the use of freshly produced detergent and disinfectants. Detailed information on agents suitable in particular for a gentle cleaning and disinfection can be requested directly from the manufacturer of the detergent and disinfectant. These are in Germany, Switzerland, for example: -
Chemische Fabrik Dr. Weigert GmbH & Co. KG, Hamburg, Germany
-
Ecolab Deutschland GmbH, Düsseldorf, Germany
-
Schülke & Mayr Zürich, Switzerland
-
Johnson & Johnson MEDICAL GmbH, Norderstedt, Germany
-
Bode Chemie GmbH & Co. KG, Hamburg, Germany
GmbH,
Norderstedt,
Germany/
All our cleaning and disinfection processes have been validated using the following agents:
The pretreatment for cleaning/disinfection has to be carried out for both methods.
Manual cleaning: CIDEZYME® Enzymatic Detergent Solution, 1.6 % v/v
It is your responsibility to ensure that the components are completely sterile when used and that
Manual disinfection: CIDEX® OPA Solution (undiluted)
• only device and product specific procedures for cleaning/ disinfection and sterilization that are sufficiently validated are used
Automated cleaning/disinfection: Neodisher MediClean forte (0.2 % – 1.0 %)
• the devices used (disinfector, sterilizer) are serviced and inspected on a regular basis • the validated parameters and/or the manufacturer’s recommended parameters are respected for each cycle Please also consider the statutory regulations applicable in your country as well as the hospital‘s hygiene requirements. This applies in particular to the various instructions for effectively deactivating prions. Medartis recommends that products are discarded when they came into contact with pathogens that are difficult to identify, such as variations of Creutzfeldt-Jakob’s disease (confirmed or suspected pathogen). Detergents, Disinfectants and Equipment Observe the following aspects when choosing detergents, disinfectants and equipment for all steps: • they must be suitable for their intended use (e.g. cleaning, disinfection or ultrasonic cleaning) • the detergent and disinfectants must be aldehyde-free (otherwise blood residues may dry and attach firmly to surfaces) • the disinfectant used must have a proven effectiveness medartis.com
The manufacturer‘s instructions, such as those regarding concentration, exposure time and temperature, must be followed. Cleaning Materials and Accessories for Precleaning/Cleaning Never use metal brushes or steel wool for cleaning Medartis products; in case of disregard the material can be damaged. Use clean, lint-free cloths (e.g. Perform classic from Schülke & Mayr) and/or soft brushes (e.g. Justman Brush from VWR International). For reprocessing cannulated products and/or products with a lumen you need materials and accessories such as cleaning stylets, bottle brushes and/or syringes with corresponding cannulated attachments. Drying Accessories Medartis recommends lint-free single-use wipes or medical compressed air. Water Regarding the water quality Medartis recommends using demineralized and purified water (e.g. Aqua purificata) for cleaning, rinsing and disinfection. High concentrations of minerals and/or contamination with microorganism, ect. can lead to spots on the products or can even prevent an effective cleaning and decontamination.
Cleaning, Disinfection, Sterilization, Inspection and Maintenance of Medartis Products l 5
For the remainder of this document, please use the following definitions regarding water temperature: Cold water: T < 40°C Warm water: T > 40°C Medartis instrument trays (steel or plastic) and implant trays made from aluminum or plastic are intended for sterilization, transportation and storage of products. They are not intended for cleaning and disinfection when loaded. The products must be removed from the trays and then cleaned and disinfected separately. Implant trays made of steel can undergo automated cleaning and disinfection when loaded. For manual cleaning/disinfection the implants must be removed from the system and cleaned/disinfected separately. 4
FLOWCHART
The individual reprocessing steps, for single-use and reusable products, are illustrated in following flowchart. More detailed information is described in the subsequent text:
5
PREPARING FOR CLEANING, DISINFECTION AND STERILIZATION
5.1
Segregating and Preparation of the Instruments after Surgery The first steps of an efficient reprocessing start in the operating room. Major contaminants, debris of agents for haemostasis, skin disinfection, lubricants and acidic pharmaceutical products must be removed before segregating dirty instruments if possible. When segregating dirty instruments consider the following aspects: instruments can be damaged (e.g. deformation of small clamps, breakage of scissor tips) by improper technique. Therefore it has to be considered that the instruments are handled carefully and properly and the instrument trays are not overloaded. Preferably use dry preparation for transportation to the cleaning/sterilization department. If a wet preparation method is used, place the instruments in a prepared solution directly after usage. Consider that: • multipart instruments (e.g. depth gauges, demountable handles, clamp sleeves of screwdrivers etc.) are disassembled as much as possible before the pretreatment; if needed, follow the assembly and disassembly instructions (see chapter 2.3 Assembling/Disassembling (Instruments)) • articulated instruments (e.g. scissors, clamps, forceps etc.) are opened as much as possible • all products (including grooves, holes, lumens, etc.) are sufficiently covered with solution in case of using a wet preparation method The products have to be prepared as soon as possible to avoid drying of blood residues or debris and to avoid damage to the materials by leaving them in the solution for longer than directed. 5.2 Pretreatment for Cleaning, Disinfection and Sterilization During manual cleaning care and attention has to be given to holes, lumens, grooves and articulated instruments! Process of the Precleaning Instruments Clean the disassembled and opened instruments under running water and: • remove visible contaminants with a soft plastic brush, e.g. Justman Brush from VWR International • shift moveable parts under running water back and forth several times and rinse them thoroughly • clean large lumina with a bottle brush by brushing them 10 times; the bottle brush has to reach the entire length of the lumen • cannulated devices (products with cavities whose diameter is less than or equal to 1/6 of the device‘s length), e.g. cannulated drills, must be treated as follows: - cleaning by inserting the dedicated cleaning stylet into the cannulated products to remove obstructions and to achieve a flow-through; the cleaning stylet has to reach the entire length of the cannulated product medartis.com
6 l Cleaning, Disinfection, Sterilization, Inspection and Maintenance of Medartis Products
- rinse the cannulated products using a suitable cannula and disposable syringe Instrument/Implant Trays Instruments always have to be removed from the trays and cleaned and disinfected separately. Clean the instrument trays (made from steel or plastic) as well under running water as follows: • if applicable remove the instruments that are still in the tray; the trays have to be empty • remove the lid if possible • clean the individual parts under running water thoroughly Clean the implant trays (made of color anodized aluminum/ plastic) as well under running water as follows: • remove the implants from the tray; the trays have to be empty • remove, if possible, the lid of the implant trays; handles must not be removed • clean the individual parts under running water thoroughly Clean the implant trays (made of steel) as well under running water as follows: • first rinse the closed implant trays thoroughly • remove the lid and rinse it separately from all sides; rinse the joints as well • rinse the opened tray with the implants from the upper side in a way that no implants can fall out After rinsing, all the products must be visually inspected; if applicable, repeat the previously mentioned precleaning procedure as required until contamination is no longer visible. In case the products are not cleaned immediately let them dry on an absorbent, clean and lint-free base (e.g. on lint-free disposable wipes, e.g. Perform classic from Schülke & Mayr). 6
CLEANING AND DISINFECTION
For the following cleaning and disinfection process the disassembled instruments and trays stay disassembled. 6.1 Manual Cleaning and Disinfection Important: For manual cleaning and disinfection, the trays have to be empty. Instruments and trays must be opened and disassembled as far as possible. Implants must be removed from the system and must be cleaned and disinfected separately. Manual Cleaning Process • Place the products in the cleaning bath with enzymatic cleaning solution for 5 minutes (e.g. CIDEZYME® Enzymatic Detergent Solution, 1.6 % v/v) It has to be considered that - the products must be adequately covered (including grooves, holes, lumens, etc.)
medartis.com
- the individual components are not in a position to damage each other - the manufacturer‘s instructions, such as those regarding, exposure time, temperature and concentration must be followed • Clean with a soft plastic brush (e.g. Justman Brush from VWR International). • During cleaning, shift moveable parts back and forth 10 times so that all areas/spots are cleaned properly. • Clean large lumina with a bottle brush by brushing them 10 times; the bottle brush has to reach the entire length of the lumen. • Cannulated devices (products with cavities whose diameter is less than or equal to 1/6 of the device‘s length), e.g. cannulated drills, must be treated as follows: - insert the dedicated cleaning stylet to remove obstructions and to achieve a flow-through; the cleaning stylet has to reach the entire length of the cannulated product - rinse the cannulated products using a suitable cannula and disposable syringe (rinsing volume: 30 ml) • Clean the products (if applicable the individual parts) in the ultrasonic bath for minimum 15 minutes; it has to be considered that - only freshly prepared solutions are used - only a suitable detergent or a combined disinfectant/ detergent is used (e.g. CIDEZYME® Enzymatic Detergent Solution, 1.6 % v/v) - the manufacturer‘s instructions, such as those regarding concentration, exposure time and temperature, must be followed - the ultrasonic bath, including rinsing and drying process of the products, is carried out corresponding to the manu facturers’ instructions • Afterwards remove the products (if applicable individual parts) from the ultrasonic bath. The following rinsing process with cold or warm water must be carried out for at least 1 minute until visible contamination is no longer evident. It has to be considered that - lumina also are rinsed inside thoroughly - cannulated products (e.g. cannulated drills) also are rinsed inside using syringes and suitable cannulas For rinsing also hand-held water jets can be used. • After rinsing with cold or warm water all products must be visually inspected; if applicable, the cleaning and disinfection process has to be repeated as required until visible contamination is no longer evident. • Let the products dry on an absorbent, clean and lint-free base (e.g. on lint-free disposable wipes, such as e.g. Perform classic from Schülke & Mayr). Manual Disinfection Process • Place the products in the disinfection bath for at least 15 minutes (e.g. CIDEX® OPA Solution, undiluted). It has to be considered that - the products are adequately covered - the individual components are not in a position to damage each other - the manufacturer‘s instructions, such as those regarding
Cleaning, Disinfection, Sterilization, Inspection and Maintenance of Medartis Products l 7
exposure time, temperature and concentration, must be followed • During disinfection shift moveable parts back and forth 10 times so that all areas/spots are disinfected properly. • Lumina have to be filled with disinfectant inside as well. • Cannulated devices (Products with cavities whose diameter is less than or equal to 1/6 of the device‘s length), e.g. cannulated drills, must be treated as follows: rinse the cannulated products with disinfectant using a suitable cannula and disposable syringe (rinsing volume: 30 ml). • Afterwards remove the products (if applicable individual parts) from the disinfection bath. The following rinsing process with cold or warm water must be carried out for at least 1 minute until all leftovers of the disinfection bath are removed. It has to be considered that - lumina also are rinsed inside thoroughly - cannulated products (e.g. cannulated drills) also are rinsed inside 3 to 5 times using syringes and suitable cannulas • Visually inspect the products and repeat the cleaning and disinfection process as required until visible contamination is no longer evident. • The products must be completely dried directly afterwards. It is recommended to dry the products using medical compressed air; this is especially gentle and effective. Otherwise lint-free disposable wipes (e.g. Perform classic from Schülke & Mayr) can be used. If applicable, the products have to be stored in a clean environment until they are completely dry. Main reasons for mechanical damages during manual reprocessing are: - metal brushes - abrasive detergents - applying significant forces - “dropping products”, “bumping products”, “tossing products” • Finally inspect the products (see chapter 7.1 “Inspection”). • Service the products (see chapter 7.2 “Care and Maintenance”). • Pack the products preferably immediately (see also chapter 8 “Packaging”) or if necessary, after giving them additional time to dry in a clean environment. 6.2 Automated Cleaning and Disinfection It is preferable to segregate dirty products using a dry method before starting the automated cleaning/disinfection process. If a wet method was used, ensure that the products have been rinsed thoroughly after pretreatment as remaining foam may reduce the rinsing pressure in washer/disinfectors and thus have a negative impact on the cleaning result. This is also valid if products are additionally processed in an ultrasonic bath. Cannulated products and lumina have to be rinsed using syringes and/or hand-held water jets. Regarding choosing and using detergents and disinfectants the information in chapter 2.4.1 and chapter 3 have to be observed. In case no thermal disinfection is used while automated
cleaning and disinfection, it has to be observed that the used disinfectant is compatible with the detergent. Medartis has used “Neodisher MediClean forte” for the validation process of the automated cleaning and disinfection and has followed the instructions of the manufacturer (instruction Dr. Weigert). The validation was carried out according to table below. When selecting the disinfector, make sure that the cleaning process includes the following phases in accordance with EN ISO 15883: Phase
Temperature
Cleaning
55°C (± 2°C) (131°F; 10 min.* ± 3.6°F)*
Duration
Action Adding detergent*
Neutralization
Cold (T < 40°C/104°F)
2 min.
Neutralize with cold water
Rinsing
Cold (T < 40°C/104°F)
1 min.
Rinse with cold water
Thermal disinfection (A0 value > 3’000)
≥ 90°C (194°F)
5 min.
With demineralized and purified water; do not add additional detergent
Dry
Device-specific (T < 141°C / 286° F)
Devicespecific
Drying process
* The information provided is based on the use of “Neodisher MediClean forte” by Dr. Weigert; validation was performed with a concentration of 0.2 % at 50°C; if a different detergent is used, exposure times, concentrations and temperatures may vary; the relevant manufacturer’s instructions must be observed. Automated Cleaning and Disinfection Process To be considered: For automated cleaning and disinfection, instruments have to be removed from the trays. Instruments have to be opened and disassembled! Implant trays made of aluminum or plastic are not intended for cleaning and disinfection when loaded. Implants must be removed from the trays and must be cleaned/disinfected separately. Implant trays made of steel can undergo automated cleaning and disinfection when loaded. Make sure the implant trays have been properly sealed with their lid prior to automated cleaning/disinfection 7
INSPECTION AND MAINTENANCE
7.1 Inspection In general sufficient cleanliness is the basic requirement for a successful sterilization. Before the products are packaged for sterilization they have to be inspected visually. (Recommendation: use working place light fixtures ideally with magnifiers).
medartis.com
8 l Cleaning, Disinfection, Sterilization, Inspection and Maintenance of Medartis Products
Instrument Inspection Check all instruments after cleaning and disinfection for damage and function. For checking the function, multi-part instruments have to be assembled (“Assembly/Disassembly Instruction”). Check the instruments for damages as e.g. for: • corrosion • damaged surfaces • fissures
Check the trays for: • corrosion • damaged surfaces • fissures • chipping • other wear • contamination
• chipping
• functionality
• other abrasion
Where contaminations remain, the products have to go through the complete cleaning and disinfection process again.
• contamination • functionality If the products are still contaminated they have to go through the entire cleaning and disinfection process again. In case of damage the instruments must be exchanged! Options for parts showing signs of corrosion, annealing colors and/or water spots: Instruments that show inacceptable signs of corrosion, annealing colors and/or water spots may be treated using an acidic cleaning concentrate for stainless steel surgical instruments such as Borer Chemie deconex® 34 GR. When doing so, the instructions of the cleaning agent must be followed. Be advised that such cleaning agents can only be used on instruments that do not contain any aluminum components. The appendix provides sample photos for damaged and/or contaminated products. During inspection the following aspects have to be considered in particular: • Thoroughly inspect critical parts such as handle structures, articulated instruments, cavities, cannulated products etc. in particular. • Instruments with lumina and cannulated products (e.g. cannulated drills) have to be checked for free passage without obstructions. Products without free passage/with obstructions have to be reprocessed. Damaged instruments have to be exchanged. • Cutting instruments (e.g. drills) have to be checked for sharpness and damages. Worn or damaged instruments have to be exchanged. • Rotating instruments (e.g. drills) have to be checked additionally for bending. This can easily be done by rolling the rotating instrument on a flat surface. Bent rotating instruments have to be exchanged. Implant Inspection Before assigning the implants to the implant containers or implant trays, check them all after cleaning and disinfection for damages and contaminations. The appendix provides sample photos for damaged and/or contaminated implants. Tray Inspection Check all the trays after cleaning and disinfection for damages and function. For checking the function multi-part trays have to be assembled. medartis.com
In case of damage the products have to be exchanged! The appendix provides sample photos for damaged and/or contaminated trays. During inspection the following aspects have to be considered in particular: • thoroughly inspect critical parts such as handle structures, articulated parts, cavities, cannulated parts etc. in particular • insure the correct and safe fitting of the lid on the tray or respective container 7.2 Care and Maintenance In general the care and maintenance procedure has to be carried out prior to functional inspection. Assemble the disassembled instruments and trays again (“Assembly/Disassembly Instructions”). Correct assembly is an absolute requirement to avoid damages and/or compromised functionality. Carefully apply maintenance products to the articulations, closures or threads and sliding surfaces e.g. scissors, clamps, etc. This is a preventative action to avoid fretting corrosion. Consider the following aspects with respect to maintenance products: • use of paraffin-based/white oil-based products • biocompatibility • the products are steam-sterilizable and steam-permeable • products containing silicone must not be used (may cause stiffness) Process • Apply maintenance products carefully to the articulations, closures or threads and sliding surfaces. • Disperse the maintenance products throughout by moving the articulating/sliding surfaces. • Remove remaining maintenance products residues with a lint-free cloth. In the case of damage or reduction of functionality of the instruments, they have to be exchanged (see also chapter 7.1 “Inspection”). 8
PACKAGING
Medartis recommends sterilizing the products in the special-
Cleaning, Disinfection, Sterilization, Inspection and Maintenance of Medartis Products l 9
ly designed sterilization containers, implant containers and instrument trays. Also single sterilization wrapping (single or double wrapping) and/or other sterilization containers can be used. If the total weight of the loaded module is over 10 kg, the module must not be sterilized in a sterilization container; rather, wrap it in sterilization paper and sterilize it in the latest manner using the approved methods. The following requirements must be fulfilled: • Accord with EN ISO 11607/EN 868-3 to 10 (so far EN 868; ANSI/AAMI/ISO 11607) • Ability for steam sterilization • Adequate protection of the implants and instruments or the sterilization packaging against mechanical damaging • Regular maintenance of the sterilization containers according to the instructions of the manufacturer 9
10
STORING
After sterilization, the products must be stored in a dry and dust-free environment. Temperature variations have to be avoided to prevent corrosive damages. The maximum storage time is dependent on different factors such as packaging, methods of storing, environment and handling. The user should define a maximal storage time for sterile products until use. Within this defined time the products have to be used or reprocessed again. 11
SYMBOLS
Symbols and their explanation are provided in the corresponding “Instructions for Use”. All relevant information can be found on the internet at: www.medartis.com/documentation/ instructions-for-use.
STERILIZATION
For the following sterilization process the disassembled instruments and trays are assembled. For the sterilization process the instructions of the appropriate sterilizers have to be followed. Steam Sterilization All NON-STERILE products can be sterilized in an autoclave. The autoclaves must be in accordance with EN285 respectively EN13060 regarding validation, servicing, maintenance and controlling. For both initial and subsequent sterilization, the following parameters were validated by Medartis in accordance with the requirements of the current sterilization standards, EN ISO 17665 and ANSI/AAMI ST79. Procedure
Fractionated and dynamic prevacuum process
Flow and gravita‑ tion processes
Exposure time
≥ 4 min
≥ 15 min.
Temperature
132°C/134°C
132°C/134°C
Drying time
> 20 – 30 min.
> 20 – 30 min.
Medartis recommends that sterilization is performed in accordance with the above validated processes. If the user utilizes other processes (e.g. flash sterilization), these must be validated by the user. The ultimate responsibility for validation of sterilization techniques and equipment lies with the user. Outside the USA: the sterilization time can be extended to 18 minutes to meet the recommendations of the WHO and the Robert Koch Institut (RKI). Medartis products are designed for these sterilization cycles. Do not use hot-air sterilization, radiation sterilization, formaldehyde sterilization, ethylene oxide sterilization or substitute procedures for sterilizing thermolabile products such as plasma or peroxide sterilization for Medartis products. medartis.com
Cleaning, Disinfection, Sterilization, Inspection and Maintenance of Medartis Products l 1
APPENDIX Contents 3
1 Screws
3
1.1
Picked-up or used (cross recess)
4
1.2
Picked-up or used (HexaDrive)
5
1.3
Locking contour screw head
5 1.4
Thread
6 1.5
Contamination/residues
7 1.6
Discoloration
8
2 Plates
8
2.1
Locking contour plate hole
8
2.2
Surface bottom of plate
9
2.3 Modification of product shape/form by user
9
2.4
10
2.5
10 2.6 11
Decoloration due to bending Decoloration due to cleaning Discoloration
3 Drills
11
3.1
Tear and wear of the cutting edges
11
3.2
Bent spiral
12
3.3
Damaged spiral
12
3.4
Untwisted spiral
13 3.5
Contamination/residues
13
Color coding
14 14 15
3.6
4 MTP Reamers 4.1
Tear and wear of the cutting edges
5 Screwdriver
15
5.1
Screwdriver blade tip
15
5.2
Damaged screwdriver blades
16
5.3
Compromised screwdriver blade/handle connection
17 5.4
Contamination/residues
18
5.5
Damaged quick coupling handles
18
5.6
Damaged quick coupling instruments
19
6 Tension Pliers
19
6.1
Lamella broken, bent or cracked
19
6.2
Clip broken, bent or cracked
20
6.3
Bent and/or contaminated lamella
medartis.com
2 l Instructions for Cleaning, Disinfection, Sterilization, Inspection and Maintenance of Medartis Products
21
7 Pliers
21
7.1
Blocked joint
21
7.2
Spring broken
22
7.3
Lost color coding
22
7.4
Deformed forceps tips
23
8 K-Wire Dispenser
23 8.1 24
9 Depth Gauge
24
9.1
24 9.2 25
10.1 Damaged saw guide
11.1 Shaped and/or used
12 Temporary Locking Stopper for TriLock Screws
27 28
Contamination/residues
11 Orbital Retractors
26 27
Needle broken, bent or damaged
10 Saw Guide
25 26
Contamination/residues
12.1 Bent and/or used
13 Instruments in General
28
13.1 Decoloration/surface damages
28
13.2 Corrosion spots
29
14 Container
29
14.1 Decoloration/surface damage
29
14.2 Damaged/broken welding seams
30
14.3 Damaged/broken lids
30
14.4 Jamming/blocked lids
31
15 Symbol Annotation
medartis.com
Instructions for Cleaning, Disinfection, Sterilization, Inspection and Maintenance of Medartis Products l 3
1 Screws 1.1 Picked-up or used (cross recess)
Possible damage – Screws which have already been picked up show deformation on the self-locking contour (red circle) Measures – Never place screws back in the set which show deformation either on the screw head or thread. They may not perform as intended – At inspection of the sets take out screws that show deformation
Unacceptable screws
medartis.com
4 l Instructions for Cleaning, Disinfection, Sterilization, Inspection and Maintenance of Medartis Products
1.2 Picked-up or used (HexaDrive)
Possible damage – Screws which have already been picked up show deformation on the self-locking contour (red circle) Measures – Never place screws back in the set which show deformation either on the screw head or thread. They may not perform as intended – At inspection of the sets take out screws that show deformation
Unacceptable screws
medartis.com
Instructions for Cleaning, Disinfection, Sterilization, Inspection and Maintenance of Medartis Products l 5
1.3 Locking contour screw head
Possible damage – Screws which have already been placed into a plate hole show deformation on the outer screw head. In general the lead-in grooves are damaged, show deformation and the anodization at that area is no longer existing Measures – Never place screws back in the set which show deformation either on the screw head or thread. They may not perform as intended – At inspection of the sets take out screws that show deformation
1.4 Thread
Possible damage – Burr formation at threads – Chip formation Measures – Never place screws back in the set which show deformation either on the screw head or thread. They may not perform as intended – At inspection of the sets take out screws that show deformation medartis.com
6 l Instructions for Cleaning, Disinfection, Sterilization, Inspection and Maintenance of Medartis Products
1.5 Contamination/residues
Possible damage Screw is contaminated with: – Blood – Bone – Other residues Measures – At inspection of the sets take out screws that show contamination
medartis.com
Instructions for Cleaning, Disinfection, Sterilization, Inspection and Maintenance of Medartis Products l 7
1.6 Discoloration
Possible damage – None Measures – A discoloration or color change has no adverse effects on the implant or its function. The protective oxide layer is fully maintained
medartis.com
8 l Instructions for Cleaning, Disinfection, Sterilization, Inspection and Maintenance of Medartis Products
2 Plates 2.1 Locking contour plate hole
Possible damage – Plate hole shows scratches, deformation and/or blank areas Measures – At inspection of the sets take out plates that show deformation – Inspection recommendation: position the plate in a slightly inclined position under the microscope in order to achieve an optimal view into the locking contour of the plate hole
2.2 Surface bottom of plate
Possible damage – Bottom of the plate hole shows deformation (red circle) Measures – At inspection of the sets take out plates that show deformation
medartis.com
Instructions for Cleaning, Disinfection, Sterilization, Inspection and Maintenance of Medartis Products l 9
2.3 Modification of product shape/form by user
Possible damage Non compliant change of the plate design: – Milling off the plate surface – Drilling additional hole(s) – Other changes to design Measures – At inspection of the sets take out plates that show deformation or other customer specific changes
2.4 Decoloration due to bending
Possible damage – Additional bending of an anatomically preshaped plate Measures – At inspection of the sets take out plates that show deformation – A discoloration or color change has no adverse effects on the implant or its function. The protective oxide layer is fully maintained
medartis.com
10 l Instructions for Cleaning, Disinfection, Sterilization, Inspection and Maintenance of Medartis Products
2.5 Decoloration due to cleaning
Possible damage – None Measures – A decoloration or color change has no adverse effects on the implant or its function. The protective oxide layer is fully maintained
2.6 Discoloration
Possible damage – None Measures – A discoloration or color change has no adverse effects on the implant or its function. The protective oxide layer is fully maintained
medartis.com
Instructions for Cleaning, Disinfection, Sterilization, Inspection and Maintenance of Medartis Products l 11
3 Drills 3.1 Tear and wear of the cutting edges
Possible damage – Drill is blunt Measures – At inspection of the sets take out damaged/blunt drill bits
3.2 Bent spiral
Possible damage – Bent spiral Measures – At inspection of the sets take out damaged/bent drill bits
medartis.com