User Manual
29 Pages
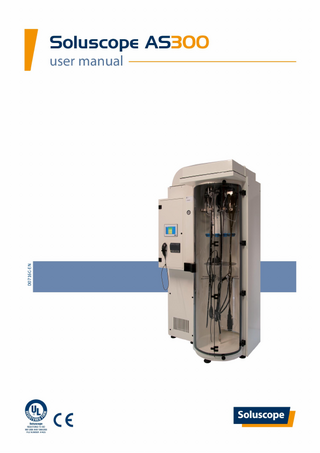
Preview
Page 1
D0716C-EN
2 This user manual provides maintenance instructions, operating instructions and warnings relating to the cabinet. It contains important information to which the user must pay special attention. Please read this user manual carefully before using the cabinet. Non-compliance with the instructions and guidelines in this user manual may result in a serious risk, health risk for, or death of, the patient and/or the operator. Never use the AS300 for any purpose other than that specified by the manufacturer. Non-compliance with these guidelines will render the manufacturer’s warranty null and void.
Please do not hesitate to contact us if you have any requirements or suggestions which could help us make our equipment safer and simpler to use. To leave a comment or make a suggestion, please visit our website, www.Soluscope.com and contact your authorised distributor. The Soluscope team
Soluscope is a registered trademark Fujifilm is a registered trademark of Fujifilm Corporation Olympus is a registered trademark of Olympus Corporation Pentax is a registered trademark of Pentax Precision Instrument Corporation © Soluscope SAS (responsible manufacturer) - Version dated 30/07/2018 100, rue du Fauge – Z.I. Les Paluds - 13400 Aubagne - FRANCE tel. +33 (0)4 91 83 21 22 • fax +33 (0)4 91 83 21 10 [email protected] All rights reserved. This documentation is protected by copyright. The copying, distribution to a third party and/or the use of this documentation is prohibited without the express written agreement of Soluscope. Soluscope reserves the right to make changes to these specifications. Please contact your authorised distributor for further information.
D0716C-EN
TABLE OF CONTENTS INTRODUCTION & OPERATOR WARNINGS ... 4 INTRODUCTION ... 4 GOOD PRACTICES ... 4 OPERATOR AND PATIENT SAFETY ... 4 CONTRAINDICATION FOR USE ... 4 SERVICING & MAINTENANCE ... 5 TRAINING ... 5 CONNECTORS & CONSUMABLES... 5 DISPOSING OF THE AS300 AND ITS CONSUMABLES ... 5 GENERAL DESCRIPTION OF EQUIPMENT ... 6 GENERAL CHARACTERISTICS ... 6 PRINCIPAL PHASES OF THE ASEPTIC UNIT ... 6 AIR CIRCULATION PRINCIPLE ... 7 ESSENTIAL FUNCTIONS... 8 CONFIGURATION OF THE STORAGE UNIT ... 9 VALID STORAGE CONDITIONS ... 10 TECHNICAL SPECIFICATIONS & OPERATING CONDITIONS ... 10 INSTALLATION & DETAILED SPECIFICATIONS ... 11 INSTALLING & CONFIGURING THE AS300 ... 11 DESCRIPTION AND USE OF THE TOUCH SCREEN ... 12 USE OF THE STORAGE CABINET AS300 ... 13 STARTUP ... 13 OPERATOR FUNCTIONS ... 13 HEAD NURSE FUNCTIONS ... 17 TRACEABILITY ... 19 MAINTENANCE ... 20 COMPULSORY MAINTENANCE ... 20 REPLACING THE INTERMEDIATE FILTER AND ANTI-DUST PRE-FILTER ... 20 REPLACING THE HEPA FILTER ... 21 IMMOBILIZATION ... 21 REPLACING THE PRINTER PAPER ... 21 FAULT INDICATION... 22 MAINTENANCE MENU FUNCTIONS ... 23 APPENDIX A. LIST OF ENDOSCOPES ELLIGIBLE FOR STORAGE IN THE AS300 ... 26 APPENDIX B. INFORMATION ON ACCESSORIES ... 27 APPENDIX C. LIST OF CONSUMABLES ... 29 APPENDIX D. IDENTIFICATION LABEL ... 29
D0716C-EN
3
INTRODUCTION & OPERATOR WARNINGS
INTRODUCTION & OPERATOR WARNINGS INTRODUCTION The AS300 is a Storage Cabinet for Thermolabile Endoscopes. The AS300 is a system used to store the thermolabile flexible endoscopes, enabling them to be maintained in aseptic conditions for several days following the last phase of the disinfection protocol applicable to this type of equipment. The AS300 storage unit is designed and manufactured in accordance with the European and national Directives and standards in force; in particular in accordance with the essential safety requirements stipulated by the provisions of Directive 2006/42/EC (Directive on machines), Directive 2014/35/EU (Directive on low voltages), Directive 2014/30/EU (Directive on electromagnetic compatibility), Directive 93/42/EC and its amendments relating to medical devices. The AS300 aseptic storage cabinet conforms to all the applicable requirements of the European standard EN16442. Endoscopes must not be stored in the AS300 unit for longer than 7 days. The list of endoscopes suitable for storage in the AS300 unit is provided by the manufacturer in appendix A to this user manual. Any endoscope not included on this list must first be validated by the manufacturer of the cabinet. The device has been designed for professional use only. It must only be used by authorized and trained persons.
GOOD PRACTICES Special attention must be given to the measures implemented to prevent the risk of handborne contamination. To obtain the required performance level, it is assumed that the endoscopes have been reprocessed to a satisfactory level of asepsis prior to storage; this is achieved by observation of the hygiene rules and the various treatment stages for the endoscopes. During set-up of your AS300, you should pay special attention to the following: • Appropriate hand hygiene when inserting and removing the endoscopes in and from the AS300: use of sterile gloves or alcohol gel; • Immediate transfer of the endoscope following treatment in the reprocessor wherever possible; • Transfer of the endoscope from the AS300 to the place of use so as not to compromise the asepsis of the endoscope: using the tray, previously cleaned and disinfected, or a sterile surgical sheet. • The installation area must be clean and well kept.
OPERATOR AND PATIENT SAFETY The AS300 must be handled by skilled personnel who have been specially trained to use this device and strictly for its use. The user must take care not to trap his/her hands when closing the door of the storage compartment. Do not remove the fixed parts or panels unless to carry out maintenance work. Such operations must be performed by qualified personnel, under safety conditions prescribed by the standards in place. The wall socket must be easily accessible by the operator. In the event of an emergency, pull out the mains plug to disconnect the AS300 from the power supply.
CONTRAINDICATION FOR USE → Do not insert equipment or instruments other than those mentioned in introduction. → Do not insert endoscopes for which the microbiological condition is not known and controlled. → Do not insert dirty endoscopes. D0716C-EN
4
INTRODUCTION & OPERATOR WARNINGS The aseptic endoscope storage unit must not be used to store endoscopes classified as critical, which must be sterilized.
SERVICING & MAINTENANCE •
The servicing and maintenance program for the AS300 is provided in detail in this user manual in chapter Maintenance. • User maintenance must be performed by an individual who has been trained by an approved Soluscope trainer. • Preventive and corrective maintenance must be carried out by either a Soluscope technician or by the distributor-technician. If servicing and maintenance are not performed, or are performed incorrectly, the operation of the cabinet, and in particular the safety of the patient and the user, may be compromised.
TRAINING There are three levels of training: Operator level: A half-day training on using the aseptic storage unit for flexible endoscopes will be provided at the time of installation on the hospital site by the technician trained by Soluscope. Head nurse level: A half-day training on calibrating and using the aseptic storage unit for flexible endoscopes will be provided at the time of installation on the hospital site by the technician trained by Soluscope. Technical service level: A half-day training will be provided to the hospital’s technical service for commissioning, calibrating and maintaining the AS300 storage cabinet.
CONNECTORS & CONSUMABLES The AS300 must be operated with its exclusively dedicated consumables. Contact your authorised distributor to obtain the list of spare parts and consumables. Connectors must never be modified. Any modification to, or replacement of the connectors may compromise the asepsis of the stored endoscopes. Connectors and tubes must receive at a minimum a high-level disinfection at least once a week: • in a Soluscope AER using the SET-AS300(00003852) adaptor, • according to the manual procedure of endoscope reprocessing. The tubes can also be sterilized. In this case the fittings must be removed and reprocessed according to the endoscope manufacturer’s recommendations.
DISPOSING OF THE AS300 AND ITS CONSUMABLES Under the provisions of directive 2012/19/UE the AS300 must not be collected by the normal household waste collection services. For European countries, please contact Soluscope or your authorised distributor to be in accordance with the regulation on electrical and electronical equipment waste.
D0716C-EN
5
GENERAL DESCRIPTION OF EQUIPMENT
GENERAL DESCRIPTION OF EQUIPMENT GENERAL CHARACTERISTICS The device is intended for storing flexible endoscopes in a controlled environment following disinfection and drying the channels according to the relevant protocol for this type of product. This objective is achieved: • By a general cycle that is both stable and aerodynamic, controlled over time using threshold information: differential pressure, humidity, temperature control, ventilation rate. • And by a principal cycle individual to each endoscope, called an aeration/channel blowing cycle. This is a connection made by the user when inserting each endoscope that provides a flow of air (4 l/min) during a pre-programmed duration for each endoscope individually. The principal cycle is critical in ensuring the coherence of the storage in relation to the manufacturer’s recommendations.
The cabinet comprises a monoblock aseptic unit, stainless steel inside and metal exterior chamber with transparent doors including two compartments: One technical front-opening compartment containing the technical components required for the functioning of the device: - Prefiltration filter (EU3/G3) - Touch screen console - Filtered air supply (EU5/G5) - Printer - Principal ventilator motor - Bar code scanner - Differential pressure switch (overpressure) - Aseptic unit/medical air connection - Automatic regulation and control - Air pressure regulator NB: The technical compartment can supply one or two storage modules (Option: AS300X2)
One or two controlled atmosphere units for storing endoscopes, comprising an easily accessible and cleanable painted stainless-steel volume, including, per unit: - Front-opening door 1/2 – 1/2 - Medical air distributor - Absolute filtration (H14) - 10 self-sealing air couplings - Differential pressure switch (filter clogging) - 10 air pressure switches - Endoscope attachment system - 10 solenoid valves (motorised and indexed carousel) - Temperature/humidity sensor - 10 removable endoscope holders AS300X2: The storage capacity can optionally be doubled (20 endoscopes) by adding a second storage module on the other side of the technical compartment. AS300 TR: The pass-through version has an additional opening in the storage compartment and allows separation of the clean area from the grey area.
PRINCIPAL PHASES OF THE ASEPTIC UNIT 1. 2. 3. 4. 5. 6.
Insertion of endoscope Launch of automatic blowing cycle Injection of medical air and unit management of aeration cycle per endoscope Removal of endoscope Routine operation on electrical compartment Maintenance operation on filter compartment
D0716C-EN
6
7
GENERAL DESCRIPTION OF EQUIPMENT 7. 8.
Emptying of machine Complete shutdown for complex maintenance work
AIR CIRCULATION PRINCIPLE Compressed medical grade air Filtered medical grade air provided by the hospital serves to blow the internal channels of the endoscope. It is channelled to the endoscopes by means of a pressure regulator, a flow control and a timed solenoid valve on a splitter incorporated into the mounting system located in the upper part of the storage unit. The endoscopes are connected to the machine via a connector specifically designed for each type of endoscope. Circulated air 100% fresh air is circulated via a grid on the front using a ventilator motor located in the technical compartment. It is blown into the storage unit where it is distributed from top to bottom. Properly calibrated extraction allows overpressure to be optimised in the storage cabinet and enables heat and ambient humidity to dissipate. Excess air is vented through a grill located at the bottom rear of the storage compartment. The rotational speed of the main fan motor is monitored when opening the storage compartment door in order to force air to exit.
Principle of blowing and treating filtered air Fresh air is distributed in the storage unit once it has been treated in a chain of filtration. It is filtered at a speed of approximately 240m³/h (=120 volumes per hour) in order to optimise the elimination of ambient humidity. To obtain overpressure (>10 Pa) in the storage compartment, the extraction rate is maintained at a lower level than the intake flow. By default, the ventilator functions at 65% of nominal flow during operation and 100% in open-door mode. A pressure switch is present to detect and resolve a failure of the ventilator motor. Aerobiodecontamination is achieved using a mechanical treatment chain procedure including: - Pre-filtration with medium efficiency filter (EU3) 80% gravimetric - Filtration with a high efficiency filter (EU5) 95% gravimetric - Absolute filtration with an ultra-high efficiency HEPA filter (H 14) 99.99 to 99,999 DOP for particles of 0.3 µ
Mounting the endoscopes and principle of blowing air into channels Endoscopes are suspended vertically in the air stream; optic in upper position on a rotating mounting plate previously equipped with self-sealing couplers connected to a timed medical grade compressed-air diffusion system. The connection to the medical air uses a silicone tube (connector) equipped with a quick-connect plug with a seal on the unit side and special, interchangeable sterilisable fittings provided by the endoscope manufacturer (c.f. appendix B Medical air connector).
FROM PISTON CAGE
D0716C-EN
FROM PROXIMAL END
GENERAL DESCRIPTION OF EQUIPMENT The mounting rotating plate is equipped with 10 removable and sterilisable endoscope holders. The mounting rotating plate is fitted with an indexed motorisation device allowing limitation of the manipulation of the endoscopes inside the cabinet. To protect endoscopes from accidental contact with each other and with the surfaces of the storage compartment as well as during handling, an optional disposable aseptic sheath may be used. A suspension is provided on the endoscope rack for this purpose. Air flow in the endoscope channel: • The endoscopes receive a fixed flow of filtered compressed air (4l/min) regardless of the number of endoscopes connected, that is why each line has a flow switch. • Compressed air only circulates during the blowing phase (60 min) and for 6 min every 4 h after that phase. • The compressed air supply is closed when coupling/decoupling the endoscope. The medical air couplings are located and numbered below each rack. OPTION: One or several variable-height shelves to hold video boxes can be optionally installed under the endoscope suspension system.
ESSENTIAL FUNCTIONS Preventing opening doors Opening the compartment door is controlled in two ways: • Control of the minimum opening time necessary to insert or remove equipment. • Determination of the reason for opening the door to avoid operator’s actions conflicting with the machine conditions. For example, it is impossible to open the door to insert an endoscope if there are already 10 endoscopes in the aseptic unit. Endoscope insertion/removal door: →It is not authorised to open the door except within standard procedure (inserting/removing endoscope) and in certain cases of maintenance to extract the endoscopes. →Door closure control if the pre-programmed time is exceeded, alarm and message display. →Closure/opening of the door by electromagnetic switch to prevent accidental blockage. The switch is triggered to prevent the operator trapping his/her fingers. Electrical cabinet door: →In maintenance mode the front of the cabinet door can be opened to enable access to the electrical and electronic modules. Lower technical cabinet door: →In maintenance mode the front of the cabinet door can be opened to enable access to the pre-filter and intermediate filter modules.
Controlling the connection to each endoscope To ensure a valid connection between the endoscope and the compressed air supply, each channel is fitted with a solenoid valve, flow control and a pressure switch: • Connection is established by reading the pressure drop upstream. • Non-connection is established by reading the pre-programmed network pressure. Each line is controlled to detect any failures (poor connection, blockage, etc.). The connections are controlled in two ways: • Visual and automatic verification of the coupling used by the operator when inserting the endoscope. • Verification of the pneumatic integrity of the line. For example, a valid coupling indicates that a stored endoscope is being blown (green light on the touch screen).
D0716C-EN
8
9
GENERAL DESCRIPTION OF EQUIPMENT Event traceability Considering the critical role of endoscopic devices in an infection control process, it is necessary to be able to provide evidence of conformity with the relevant standards for events occurring individually on each endoscope having passed through the aseptic storage unit. In a ranked and operational manner, a ticket is produced in a single or duplicate copy when each endoscope is removed. The information provided includes the identification of the operator inserting and removing the endoscope, the date and time of entry and removal as well as conformity with the recommendations or, where appropriate, of non-conformity including the main reason for non-conformity. A printer returns recorded parameters for insertion, storage and removal of each endoscope. These parameters are also saved on a memory card installed on the back of the control panel.
CONFIGURATION OF THE STORAGE UNIT STORAGE UNIT A – Transparent doors B – Electrical cabinet C – Touch screen D – Door of the filter compartment E – Compressed medical air connector F – Filter cabinet H14 (single or double) G – Rotating endoscope rack AIR TREATMENT CIRCUIT 1 – Fresh air entry 2 – Pre-filter for fresh air EU 3 (80% gravimetric) 3 – Filtration EU 5 (95% gravimetric) 4 – Centrifugal variable output ventilator 5 – Flow stabilisation cone 6 – Air distribution cabinet 7 – High-efficiency H14 filter (99.99 DOP for particles of 0.3μ) 8 – Air extractor
Additional storage unit
Storage unit for 10 endoscopes
The storage unit circulates a constantly renewed flow of filtered, optionally heated air, distributed using a unidirectional vertical piston in the endoscope storage zone. This area comprises a horizontal motorised plate supporting a maximum of 10 endoscopes suspended vertically. The storage area is accessed via a door providing access to only one free space per endoscope (when inserting) or one endoscope (the one selected for removal). The relevant space is presented to the operator by the motorized rotation of the rack plate. The plate receives all 10 functions associated with the principal blowing cycle for endoscope channels by means of connection to a local medical grade compressed air distribution network, that is, the couplings of each section and the continuous control of the presence of the coupling. The aerodynamic unit maintains the endoscopes in a controlled environment using a set of upstream filters controlled at the time of use and a high-efficiency downstream filter which is controlled against clogging using a differential pressure switch. All parameters, functions and cycles are monitored and controlled automatically. Operation tasks are managed using a touch screen with dedicated functions which does not require calibration by the operator except for installation and commissioning on site. D0716C-EN
10
GENERAL DESCRIPTION OF EQUIPMENT VALID STORAGE CONDITIONS
Removing an endoscope will render the cycle invalid if: • The maximum storage time has been exceeded (set in the Settings menu: maximum value 7 days) • The air supply has been interrupted during the channel blowing cycle • The blowing time for the channels has not been respected (set in the Settings menu: minimum value 60 min) • The power supply has been interrupted since inserting the endoscope in the cabinet • There has been excess humidity and/or temperature while the endoscope was present in the cabinet (set time and alarm threshold in the Settings menu) • The door has been open for too long while the endoscope was present in the cabinet (set time and alarm threshold in the Settings menu) • There has been a filter failure while the endoscope was present in the cabinet (pressure threshold exceeded) • The cabinet has been emptied while the endoscope was present in the cabinet Any one of these conditions renders the storage invalid. Endoscopes present in the aseptic unit when an alarm is triggered are associated with this alarm.
TECHNICAL SPECIFICATIONS & OPERATING CONDITIONS Dimensions (L. x D. x H.) Empty weight Consumption of medical air at full load Recommended blowing time (channels) Medical air connection Minimum/maximum air pressure Grade of compressed air Supply voltage Power supply Electrical connection capacity Operating temperature Storage temperature Use Altitude Pollution degree Relative humidity Overvoltage category
D0716C-EN
Simple cabinet 107 x 70 x 235 cm 300 kg
Double cabinet 184 x 70 x 235 cm 450 kg
Pass-through cabinet 110 x 80 x 217 cm 286 kg
40 l/min
80 l/min
40 l/min
60 minutes Normalised > 2 bar and < 7 bar Medical grade filtered air in accordance with standards in force 220/240V – 50 Hz 600 W 10 A (oscillating if possible) from 15°C to 30°C (59°F – 86°F) (humidity 70%) from 5°C to 50°C (41°F – 122°F) Indoor <2000m 2 <70% Category II
11
INSTALLATION & DETAILED SPECIFICATIONS
INSTALLATION & DETAILED SPECIFICATIONS The following information is provided to ensure the correct operation of your AS300. If this information is not observed, cycle performance may be modified, resulting in damages that will not be covered by the manufacturer’s warranty. We recommend that you leave the AS300 switched on permanently (display lit). If the AS300 is switched off for a long period, please contact your authorised distributor. For its initial operation, all interior surfaces of the cabinet must be cleaned thoroughly using a surface cleaning and disinfecting solution. Never place any objects on top of the cabinet. In the event of an emergency, pull out the mains plug to disconnect the AS300 from the power supply.
INSTALLING & CONFIGURING THE AS300 Installation The AS300 must be installed by a qualified Soluscope technician and its installation must be validated by the installation conformity statement supplied with the AS300. This document constitutes proof of installation qualification and validation. It is important to position the storage unit to ensure sufficient space for normal operation, use and maintenance:
SINGLE CABINET
DOUBLE CABINET
The overall height is 235 cm for AS300V2 and AS300x2 versions.
The overall height is 217 cm for AS300 TR version. Ensure minimum space of one meter in front of the storage unit to facilitate use. The AS300 must be installed close to where the endoscopes are disinfected, in a location appropriate for use such as an endoscope decontamination room. For technical or operational reasons, it is preferable that clean areas are located within clean rooms. Users should manage the flow of personnel and equipment in such a way as to prevent the risk of contamination when moving from one area to another. The AS300 unit is portable and sits on 8 feet the height of which can be adjusted. It is not necessary to attach the device to the wall or floor. Your electrical installation must be connected to the main earth terminal of the building at 1 wall socket: 220240 V + earth 50 Hz 16A via a dedicated power supply cable for the AS300. D0716C-EN
INSTALLATION & DETAILED SPECIFICATIONS
12
The storage unit is equipped at the rear with a flexible cable for connection to the filtered medical grade air source. A normalised supply of medical grade air must be installed close to the storage unit. Installation qualification includes: • Verification of the environment for the functioning of the unit (air, power supply). • Physical check including parameters and all functional and alarm tests. • Provision of a technical manual to the medical technician. • Training of personnel using the machine.
Configuration After checking that the cabinet functions correctly, the qualified Soluscope technician will configure various parameters, such as: • the date and the time, • The process settings (maximum storage time, fan speed, etc.) • user names, • the list of endoscopes which will be stored in the cabinet, Please ensure that the technician has the support of a person who will be in charge of providing the elements required to install the unit correctly.
DESCRIPTION AND USE OF THE TOUCH SCREEN User levels For safety reasons, the various cabinet functions are accessed according to secure user management (user name + passwords). Passwords correspond to different access levels and these passwords will be provided during installation and according to your user level. ADMIN Administrator = Qualified Soluscope technician MAINTENANCE Soluscope technician or a technician at your hospital who has been trained by a qualified Soluscope person HEAD NURSE Chief Nurse at the hospital OPERATOR Nurse A badge containing identification information is assigned to each operator. It is read by a bar code reader (or RFID in option) positioned on the door of the technical compartment.
Use of the touch screen The types of endoscope are pre-recorded in the machine. When inserting an endoscope, the operator selects the relevant endoscope reference from a drop-down menu on the touch screen. It is possible to remove an endoscope during a ventilation cycle without compromising the storage quality. It is not possible to remove an endoscope during a channel blowing cycle without compromising the storage quality (invalid cycle).
D0716C-EN
USE OF THE STORAGE CABINET AS300
13
USE OF THE STORAGE CABINET AS300 STARTUP A start-up procedure must be carried out the first time the AS300 cabinet is used and every time it is powered on. This operation calibrates the sections of the endoscope rack plate. Proceed as follows: 1. When switching on power to the cabinet, wait until the start-up process on the touch screen is completed. 2. Confirm reading the error messages that appear in the window in the foreground by pressing as many times as necessary. 3. After having read all the error messages, start the identification process using the barcode reader (or RFID system). 4. Press the Operator Menu on the top of the touch screen. 5.
Press « start up cabinet ».
6.
Wait for the start-up procedure to end. When the process is finished, the button turns green.
7.
Press on this button to return to the main screen.
OPERATOR FUNCTIONS Recommendation: Prior to and while handling endoscopes in the context of the storage procedure and in particular when inserting and removing, it is recommended to sanitize the hands according to the applicable protocol. Please note that it is necessary to reduce the time between the end of the cleaning/disinfection cycle and the beginning of storage in the aseptic unit in order to reduce the risks of environmental contamination. This time must not exceed 25 minutes. At the end of the standard disinfection protocol, place the endoscope on a clean surface on which you have prepared the disinfected connector dried with medical or compressed air and if applicable also the aseptic sheath for the treated endoscope.
Storage / Blowing phase During the storage/blowing phase, the home screen looks like this: The clear green sections indicate occupied positions in the blowing phase The dark green sections indicate endoscopes for which the cycle is valid (blowing complete) The orange sections indicate endoscopes for which the cycle is close to being invalidated The red sections indicate endoscopes for which the cycle is invalid (e.g.: maximum storage time exceeded) The yellow sections indicate empty positions.
Simply pressing the symbol next to the occupied section brings up information relating to the identification of the equipment, date and time of insertion and presence time in the AS300:
D0716C-EN
14
USE OF THE STORAGE CABINET AS300 Inserting an endoscope Purge the channels and dry the endoscope using medical or compressed air.
For endoscope drying, purge each channel with medical or compressed air by placing the distal tip above an anhydrous copper (II) sulphate paper (or alternatively blotting paper). Purge each channel until no residual water traces come from the distal tip. Apply the same procedure for connector drying.
Since certain AERs do not control the proper irrigation of the channels during the disinfection process, check at this stage that all the endoscope channels allow the air to flow freely before inserting it in the cabinet. 1. 2.
If using aseptic sheaths, open the protective envelope of the aseptic sheath and unfold it. Insert the distal end (insertion tube) of the endoscope into the sheath up to the control handle. Unfold the connector and connect the different connectors to the endoscope connection points. Check that the silicone tube is not pinched. It is recommended to check that air can pass freely through the connector to the endoscope connection points using a medical air gun before connection.
3.
Start the identification process using the barcode reader (or RFID system) and the badge associated with the Operator level. After the beep, screen 1 appears.
4.
Select the reference of the endoscope to be inserted from the list by pressing the relevant button.
5.
Wait for the carousel to come to a stop and the door to open automatically. (Screen 2)
6.
Insert the pre-connected endoscope into the AS300 cabinet on the section of the rack presented when opening the door. Mount the endoscope vertically with the optic in the upper position. The sheath and the connection cable to the cold light should hang down each side of the rack without touching the bottom of the storage compartment. Then connect the connectors to the air supply located on the central cylinder underneath and to the right of the holder. Visually check that air is circulating freely. Then fix the aseptic sleeve onto the dedicated position.
7.
SCREEN 1
SCREEN 2
Close the door and ensure that the carousel returns to its original position. SCREEN 3
If air does not circulate in the endoscope channels, this can increase the risk of bacterial proliferation. In this case you must remove the improperly connected endoscope and reinsert it. If you connect a different endoscope than the one intended to be on this position, the cabinet will not detect the error. This will result in incorrect traceability for both endoscopes (the one intended to be connected and the one connect instead). Check connection between connectors and the endoscope before closing the door.
D0716C-EN
15
USE OF THE STORAGE CABINET AS300 Removing an endoscope 1.
2.
Start the identification process using the barcode reader (or RFID system) and the badge associated with the Operator level. After the beep, screen 1 appears. Select the reference of the endoscope to be removed from the list by pressing the relevant button. When handling and in particular when inserting and removing endoscopes we recommend that you wash and sanitize your hands according to the applicable protocol.
3. Wait for the carousel to come to a stop (screen 2) 4. Validate if the model is correct (screen 3) The selected endoscope is automatically presented in front of the door. Open the electromagnetic door lock. 5. Disconnect the connector from the central cylinder; detach the selected endoscope with the connectors still attached. 6. Close the door.
SCREEN 1
SCREEN 2
Endoscopes must be removed one after another. Never remove more than one endoscope at a time. The validation ticket will be printed automatically. At this stage it is important to check again that all the connections for irrigating the internal channels of the endoscope are still connected to the different points on the endoscope. If not, the storage cycle must be considered invalid.
SCREEN 3
Screen 4 appears automatically while the validation ticket is being printed. This screen appears for 20 seconds and is then refreshed for the following endoscope removal. Cycle valid = disinfection. Cycle invalid =
the endoscope can be used without repeat the endoscope must be disinfected again.
SCREEN 4
It is impossible to interrupt the removal operation once the electromagnetic door lock is released. In the event of an error during removal: • Removal of an endoscope not corresponding to the selected position • Incorrect disconnection of the medical air supply connection When closing the door, the message « endoscope not properly disconnected » appears: 1. Reconnect the endoscope removed by mistake and disconnect the endoscope corresponding to the initial choice. 2. Check that the end of the connector is not still connected to the coupling. 3. Close the door.
D0716C-EN
USE OF THE STORAGE CABINET AS300
16
Operator Menu Start the process of identification using the barcode reader (or RFID system) and the badge associated with the Operator level.
EMPTYING THE CABINET Button to start the complete emptying procedure of the storage compartment. This procedure must be started if you need to access the endoscope inventory following a system failure or before launching a cleaning protocol. 1. Open the door. 2. Remove the endoscopes one by one from their positions and disinfect them. 3. Pressing the door contact for a few seconds enables the plate to rotate, providing access to all endoscopes. A ticket is automatically printed with the operator name and the date and time as well as the list of all endoscopes in the cabinet. CLEANING THE UNIT Button to start a unit cleaning protocol This procedure must be carried out for the quarterly cleaning of the storage compartment and endoscope rack. If the storage compartment is not empty, proceed to empty it or to remove all the endoscopes. Pressing the door contact enables the plate to rotate thus providing access to all hangers two by two. Continue until all the hangers are removed. At the end of the procedure the door will remain open for cleaning procedure. When cleaning is done press the door contact to re-introduce the hangers two by two. Follow the instructions on the screen. A ticket is automatically printed with the operator name, date and time of cleaning. CALIBRATING THE SCREEN This button allows starting a screen calibration protocol. Follow the instructions on the screen.
CLEANING THE SCREEN This button deactivates the touch screen functions. Wait for the grey band to scroll on the screen. Automatically returns to the home screen. EXIT Press to return to the home screen.
D0716C-EN
USE OF THE STORAGE CABINET AS300
17
HEAD NURSE FUNCTIONS At the time of commissioning and whenever necessary when using the AS300 cabinet, certain functional parameters must be set. These operations enable: the identification of personnel authorised to use the storage cabinet, the identification of material prior to storage, setting the time.
Head Nurse menu Start the identification process using the barcode reader (or RFID system) and the badge associated with the Head Nurse level.
USER REGISTRATION Setting authorised users Users are listed in alphabetical order. The maximum capacity is 50 users. Users are divided into four groups with restricted access according to the level: • Administrator level: Reserved for a Soluscope technician • Maintenance level: Access restricted to technical and operator maintenance functions • Head nurse level: Access to settings and operator menus • Operator level: Authorised access limited to insertion and removal functions To add a user: When the list on the screen is full, press the navigation bar on the right of the screen and select the last empty box at the bottom left in the User column. • Perform TWO DOUBLE CLICKS on the empty box in the User column until a white box appears. Using the alphanumeric keyboard, type a name or abbreviation printed on the ID badge and validate: • Perform TWO DOUBLE CLICKS on the empty box in the Password column, scan the badge corresponding to the name or icon selected. Confirm the password by scanning a second time. • Press the Group box to display the drop-down menu, select the access level to attribute to this user. Editing/deleting a user D0716C-EN
18
USE OF THE STORAGE CABINET AS300 •
•
To edit or delete an existing user, press the scroll bar at the right of the screen to scroll though the list of users. Select the box to edit, perform two double clicks on the User box and delete the ID icon by pressing then validate by pressing The user is then deleted from the list. Enter the new parameters according to the same procedure.
DATE & TIME SETTING Enter the time format hh:mm:ss using the numeric keyboard then press
to validate.
Repeat the same operation for the date. The setting operation is no longer accessible once an endoscope has been inserted into the storage unit (clock with red background) ENDOSCOPE NAMES From the drop-down menu (upper window) select the position of the endoscope to register or edit then press
Press the yellow “Name of endoscope” button Using the alphanumeric keyboard, type a name or abbreviation and validate This icon will be the ID name of the endoscope in this position.
DISABLE LINE This function allows a rack position to be disabled following a problem with the endoscope affected to this position, such as an endoscope identified as in need of repair or for which the microbiological quality prior to storage is uncertain. The activation of this function locks all access to the affected rack position for the time necessary to resolve the problem. • • •
Press the reference of the endoscope to be disabled. When the reference flashes red, exit the function. Disabled positions are marked black on the screen.
EXIT Press to return to the home screen
D0716C-EN
USE OF THE STORAGE CABINET AS300
19
TRACEABILITY Ticket printout The ticket includes all the storage traceability information: • Endoscope reference • Identity of operator inserting endoscope • Identity of operator removing endoscope • Date and time of entry and removal of endoscope • Duration of presence in the unit • Validation or invalidation of storage cycle with identification code of incident causing invalidation if applicable The codes appear in the same sequence as the one shown on the touch screen when performing an endoscope withdrawal. • Red screen display: storage duration: invalid Printed Code 100000 means storage duration exceeded • Red screen display: medical air: invalid Printed Code 010000 means air inside channels default • Red screen display: connection: invalid Printed Code 001000 means invalid connection • Red screen display: door opening: invalid Printed Code 000100 means door stayed open too long • Red screen display: ventilation: invalid Printed Code 000010 means ventilation default For each of those defaults the screen becomes red and the specific default is pointed out on the screen. The user may not reuse an endoscope when the screen is red.
Removable memory card Two Excel files are accessible: A historical file detailing the transit of endoscopes: • Date and time of insertion • Name of operator inserting the endoscope • Date and time of removal • Name of operator removing the endoscope • Incident: none or historical file of functional incidents All information relating to critical incidents that may happen while the storage unit is in operation are also stored in a specific file on the memory card.
D0716C-EN
20
MAINTENANCE
MAINTENANCE COMPULSORY MAINTENANCE Critical maintenance operations are generated by the PLC and displayed on the home screen.
Weekly maintenance ➔ Clean the bottom of the tank of the storage unit with a cloth soaked in disinfectant. ➔ Clean the screen using a compress soaked in alcohol in screen cleaning mode (c.f. Operator menu section Cleaning the screen).
Quarterly maintenance ➔ Thorough cleaning of internal surfaces of the storage compartment using a cloth soaked in contact disinfectant in unit cleaning mode (c.f. Operator menu section Cleaning the unit). ➔ Clean the endoscope hangers by soaking in disinfectant solution.
Semi-annual maintenance ➔ For AS300V2 and AS300x2 versions: change the intermediate filter and the anti-dust pre-filter ➔ For AS300TR version: change the combined pre-filter
Annual maintenance ➔ Meet with your technician trained by Soluscope in order to perform preventive maintenance: check pressure, flow, temperature and humidity gauges. ➔ Change absolute terminal filter.
REPLACING THE INTERMEDIATE FILTER AND ANTI-DUST PRE-FILTER This procedure is performed by technicians during the semi-annual maintenance. Before changing the filters, deactivate the alarm via the maintenance menu on the touch screen.
STEP
STEP
1
Open the front filter compartment with the special key
STEP
Close the compartment with the special key
4 STEP
5
2
Remove the 2 filters from their position
Activate the alarm for filter compartment and reset the counters via SETTING in the Maintenance Menu
D0716C-EN
STEP
3
Insert new filters as far as they will go
Make sure that the arrows on the label are pointing upwards.